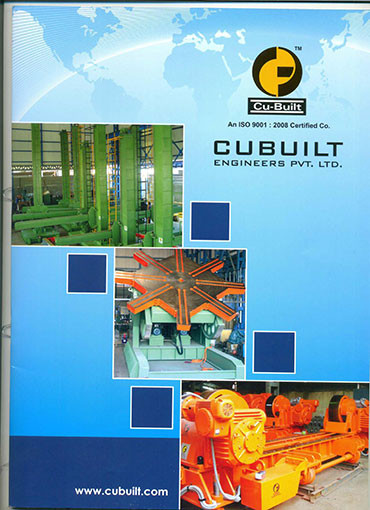
Download Broucher
Welding Automation Systems Manufacturing
Welding is the most complex process of manufacturing and is often the least understood. A large number of companies are spending millions of dollars automating production while skipping the method of welding. For many assemblies, manual welding is still the best process. To order to increase efficiency, output, and competitiveness, most assemblers introduce automatic welding systems.
A prototype machine or set of machines loads
A prototype machine or set of machines loads the workpiece in fully automatic welding, ranks the component or torch in place, conducts welding, controls the joint performance, and unloads the finished product. When required, external items in position and final product quality controls may also be built into the system. A machine operator may be expected depending on the service.
Welding Automation Systems Advantages
The four major advantages of automated welding systems: enhanced welding efficiency, improved production, lower scrap and reduced labor costs. Automated welding systems ensure weld integrity through electronic weld process controllers. The defects are easily visible and observable because a weld is only made once. Semi-automated and fully automated systems increase the output of the welding process by reducing the human aspect. Welding automation systems can easily surpass a skilled manual welder with reduced setup time and higher welding speeds. Relying on human welders will significantly increase the labor cost of a supplier. Manufacturers must consider the hours spent on manufacturing assemblies while planning for labor costs.